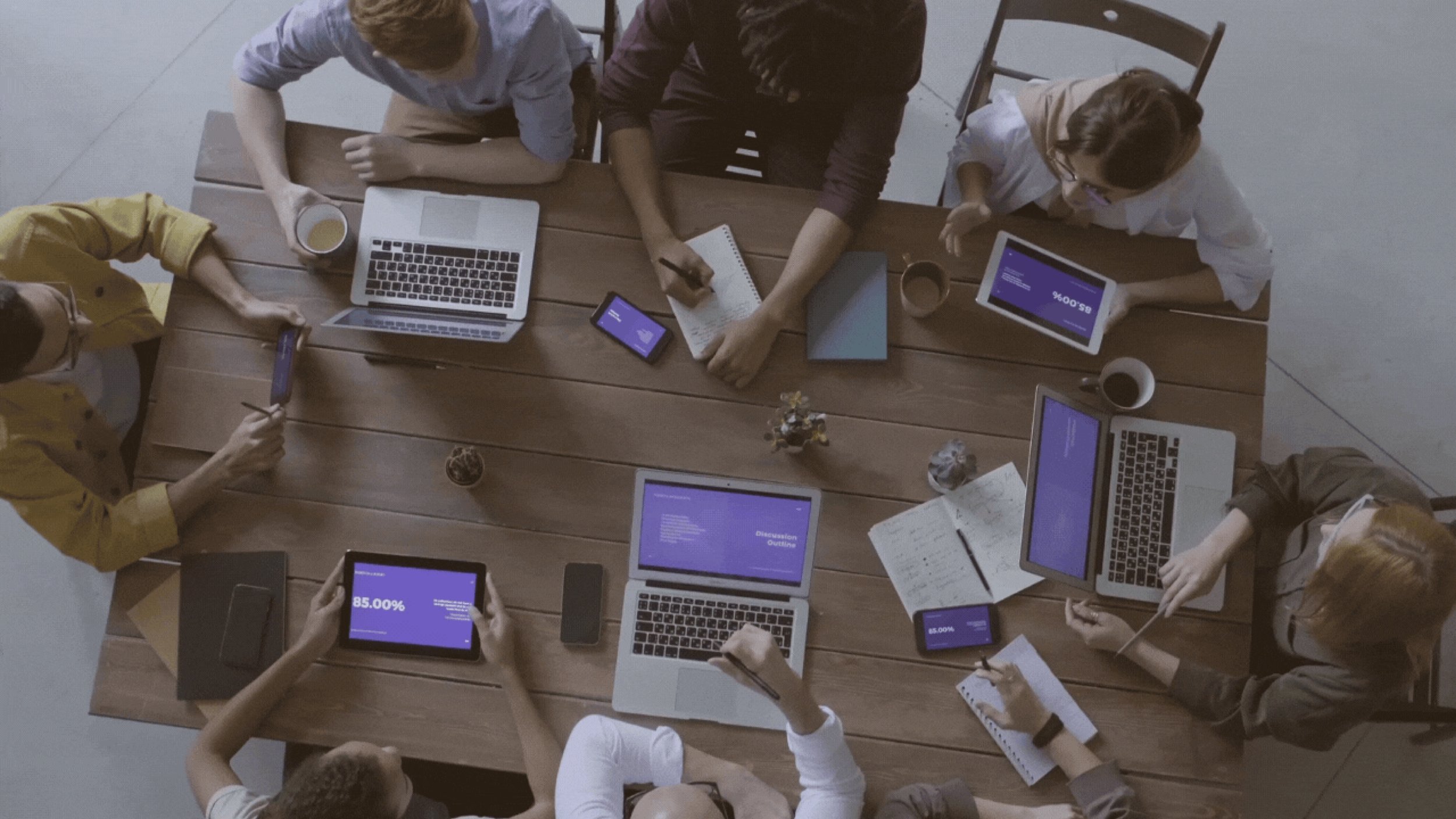
Process Improvement FAQ: Everything You Need to Know
What are Process Improvements?
Process improvements refer to strategies and methodologies used to make business operations more efficient, effective, and scalable. Whether it’s reducing waste, improving quality, or streamlining workflows, process improvement helps businesses work smarter, not harder. If you're a Manager or Director trying to navigate process improvement for the first time, this FAQ will help answer key questions and provide a solid foundation for getting started.
FAQ
-
Process improvements involve identifying inefficiencies in a business workflow and implementing strategies to enhance productivity, reduce waste, and improve quality. They can be small changes or large-scale transformations, depending on the organization’s goals.
-
Process improvement helps companies save time and money, increase customer satisfaction, and maintain a competitive edge. By refining workflows and eliminating inefficiencies, businesses can achieve long-term success.
-
While the two terms are closely related, process improvement generally refers to refining specific workflows, whereas business process improvements often involve larger, organization-wide changes aimed at optimizing overall operations.
-
The most common methodologies include Lean, Six Sigma, Total Quality Management (TQM), and Business Process Management (BPM). Each approach has different principles but shares the goal of improving efficiency and quality.
-
Many businesses use a combination of these methods to achieve their goals:
Lean focuses on eliminating waste and maximizing value.
Six Sigma emphasizes reducing errors and variations using data-driven analysis.
TQM promotes a company-wide focus on continuous improvement and customer satisfaction.
Learn how to apply the most common methodologies to everyday use cases in this side-by-side comparison.
-
A process improvement plan is a structured approach to identifying and addressing inefficiencies in a workflow. It typically includes:
Defining the problem
Analyzing the current process
Identifying solutions
Implementing changes
Measuring results and making further improvements
Six Sigma methodology approaches process improvement with their DMAIC framework (Define, Measure, Analyze, Improve, Control).
-
Start by mapping out workflows, identifying bottlenecks, and collecting feedback from employees and customers. Using tools like Process Mapping or Root Cause Analysis can provide deeper insights.
-
Strong analytical thinking, problem-solving, project management, and collaboration skills are essential for driving successful process improvements.
-
BPM is a structured approach to optimizing processes by modeling, analyzing, and continuously improving them. It helps organizations become more agile and efficient.
-
Key performance indicators (KPIs) like cycle time, error rates, customer satisfaction, and cost savings can help evaluate the impact of process improvements.
-
Popular tools include Lean Value Stream Mapping, Six Sigma DMAIC, Process Mapping tools, and workflow automation software like BPM platforms.
-
Regularly monitor performance, gather feedback, and adjust strategies as needed. Encouraging a culture of continuous improvement ensures long-term success.
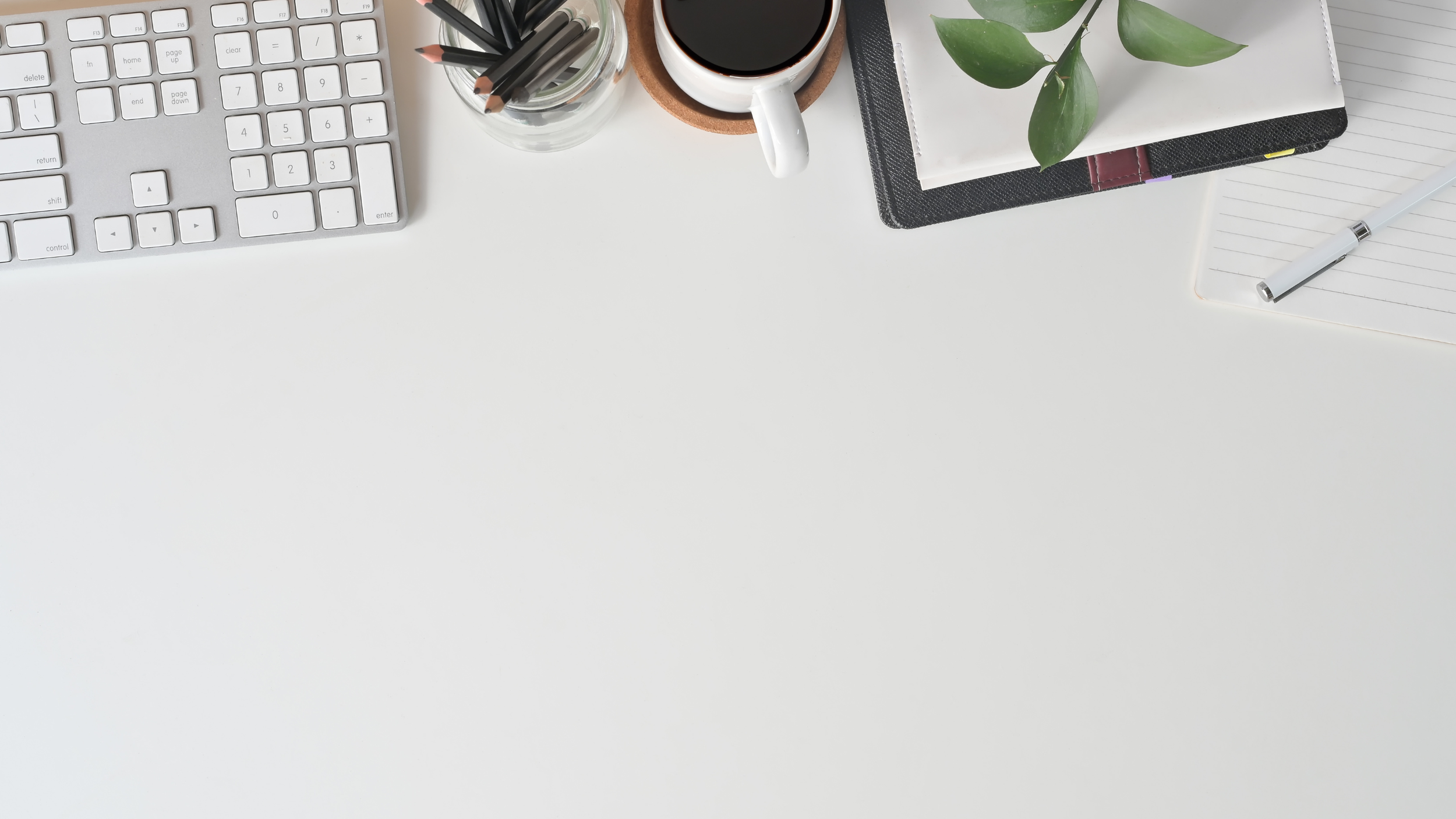
Ready to Optimize Your Processes?
Process improvement isn’t just about fixing problems—it’s about building a more efficient and resilient business. If you're ready to take your processes to the next level, explore our Glossary of Process Improvement Terms. Still lost? We’re here to help.